Maximize the potential of your wagon fleet with dynamic rail asset management
From real-time tracking to maintenance planning: Make your wagon management safer, more reliable and more cost efficient.
Where is each wagon of my fleet, and what is their current state?
Lack of real-time visibility
Without accurate, real-time tracking, it becomes challenging to locate and monitor wagons, leading to inefficiencies and delayed decision-making.
Inefficient maintenance scheduling
Poor planning and tracking of maintenance activities result in unexpected breakdowns, increased downtime, and higher costs.
Fragmented data management
Disparate systems for wagon information, rental contracts, damages, and availability hinder seamless operations and data consolidation.
Ineffective utilization of assets
Limited insights into wagon availability, mileage, and usage patterns prevent optimal asset utilization, increasing idle time and costs.
Delayed incident response
Without timely alerts for wagon events, issues like damages or route deviations go unnoticed, compromising safety and operations.
Optimize the utilization, maintenance, and operation of your wagon fleet.
Real-time fleet tracking
Use GPS and multi-source tracking to monitor the location, condition and availability of vehicles on an interactive map for precise control.
Automated maintenance management
Leverage dashboards, alerts, and scheduling tools to pilot maintenance activities, track histories, and prevent unplanned downtime.
Centralized wagon referential
Digitize and integrate all wagon-related data (rental contracts, damages, mileage, etc.) into a unified system for easy access and management.
Proactive event alerts
Configure event-based notifications to receive instant updates on wagon status changes or geofence breaches for rapid incident resolution.
Advanced inventory monitoring
Display and manage wagon availability, state, and min/max thresholds in real-time to improve asset utilization and streamline operations.
Centralized, integrated and proactive: How Fleet Efficiency optimizes rail asset management for seamless operations.
Always know where your wagons are: Track your fleet on a map in real time, to monitor trips, retention and incidents.
Lack of centralized and proactive wagon monitoring leads to inefficiencies, delays, and operational blind spots.
Fully utilized wagon capacities allow you to:
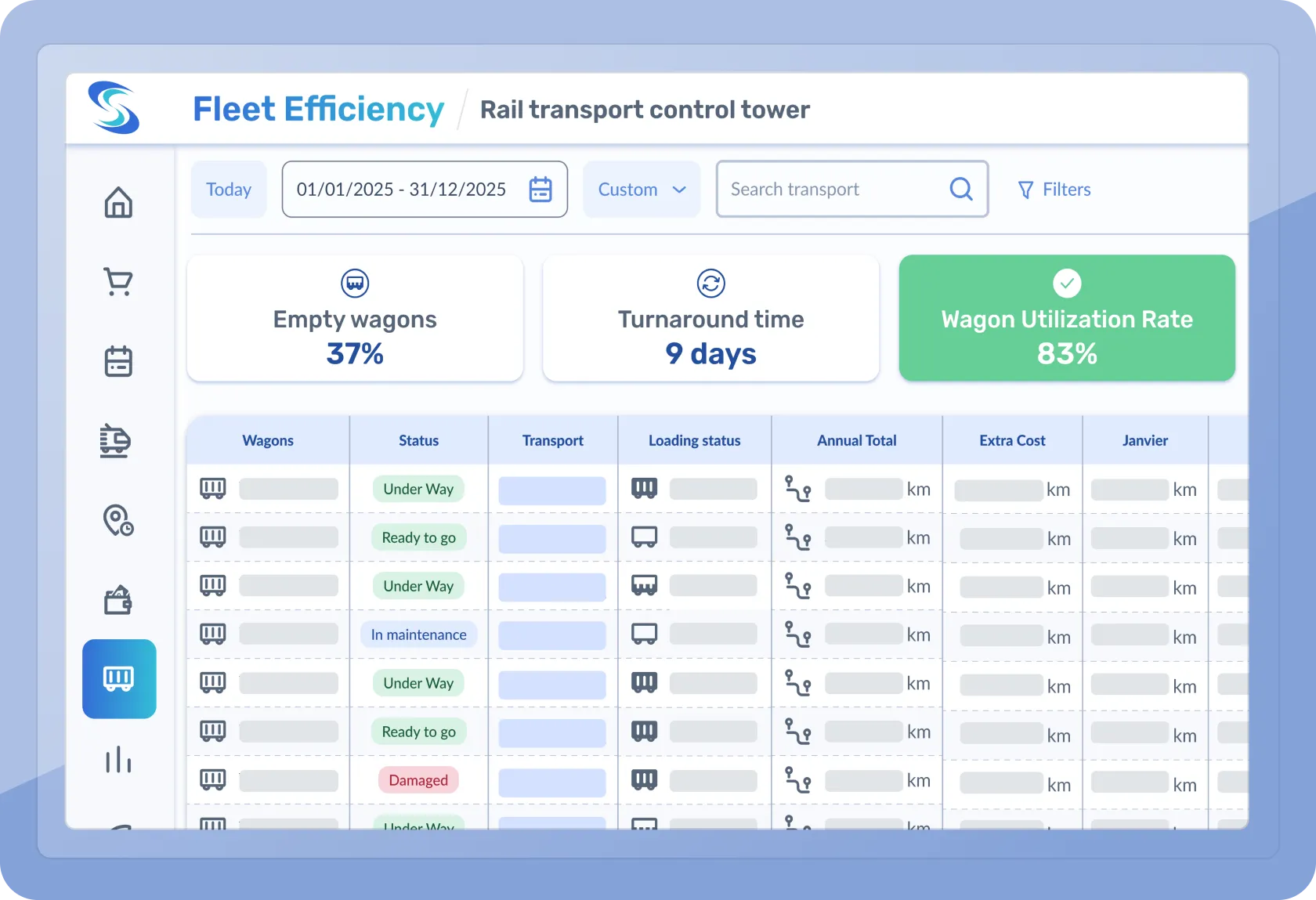
Inability to accurately forecast and monitor wagon availability leads to inefficient fleet utilization, planning issues, and operational delays.
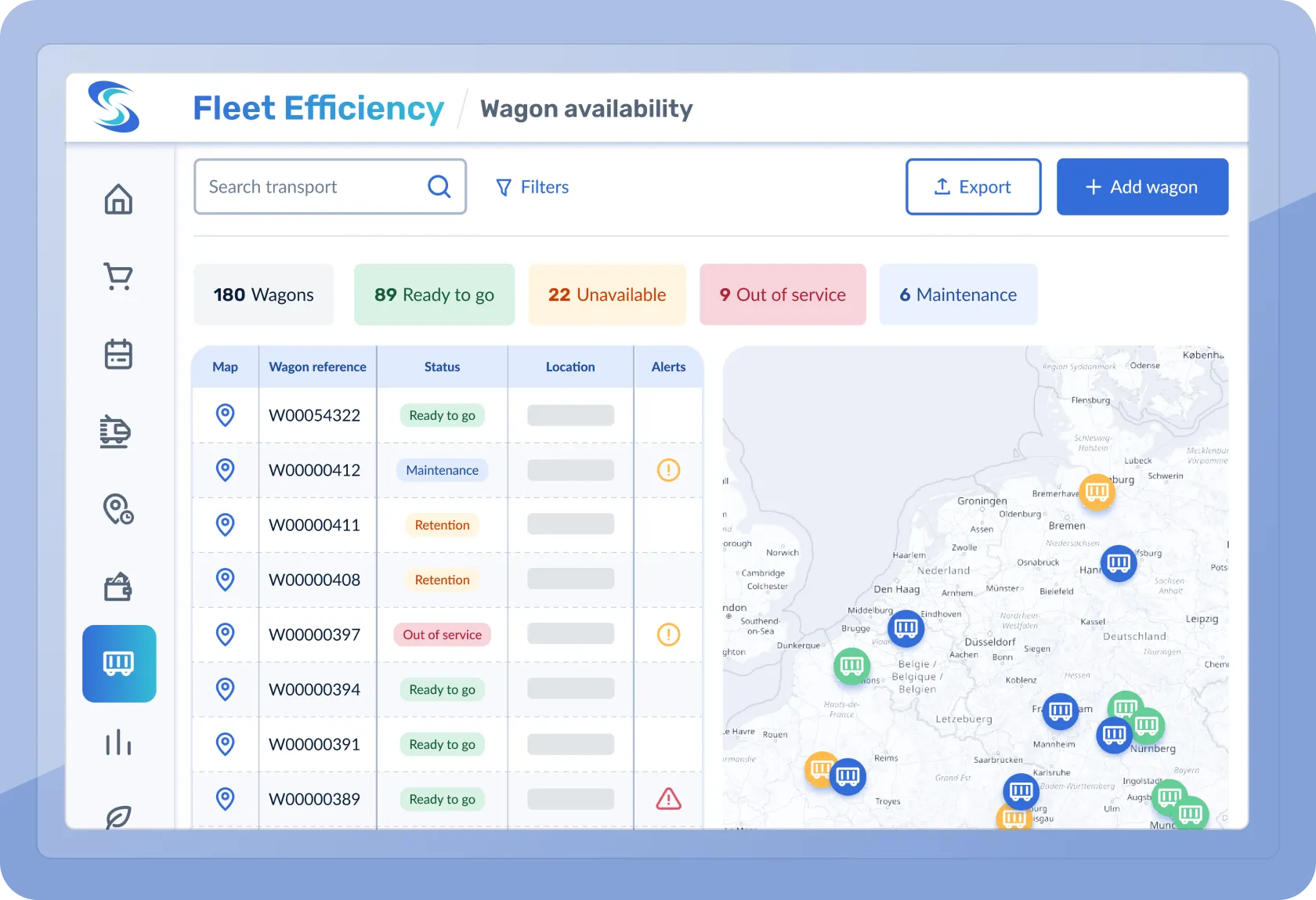
What happens if your wagon inventory is based on outdated data?
A comprehensive real-time view of your wagon availability is provided by the following enablers:
Lack of centralized and proactive maintenance management for wagons results in increased downtime, inefficiencies, and safety risks.
Poor visibility over your wagon maintenance means you'll spend more on your rentals:
Streamlined wagon maintenance means:
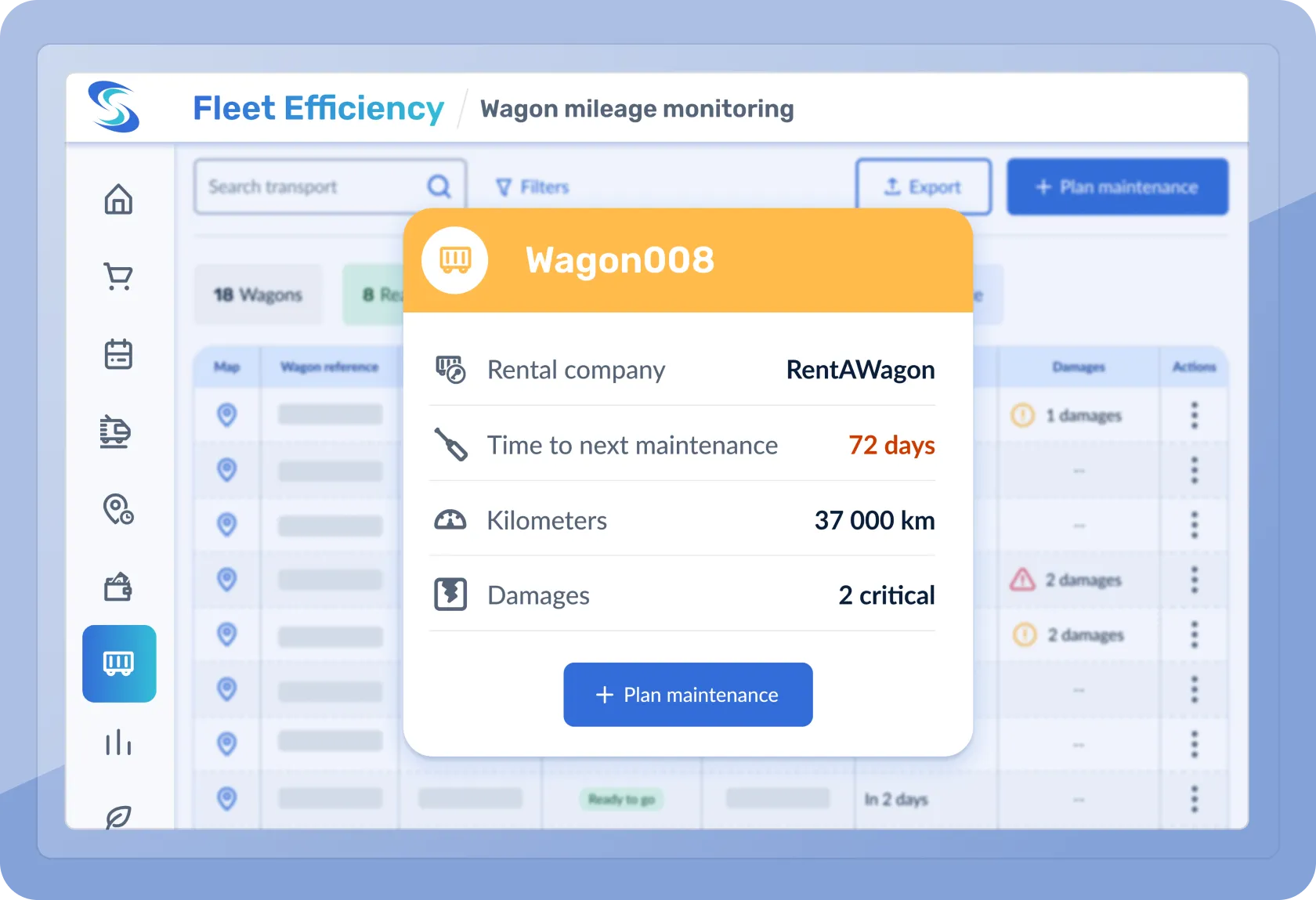
Take it from our clients
Meet the driving forces that transform the rail freight industry
Hesitations?
Let’s clear them up!
Everything you need to know about Fleet Efficiency.
How does Fleet Efficiency contribute to cost savings?
By optimizing fleet utilization, reducing downtime, preventing over-maintenance, and providing insights for better resource allocation, the module significantly lowers operational costs.
What kind of wagon information can I digitize and track with Fleet Efficiency?
You can digitize details like wagon type, rental contracts, dimensions, tare weight, mileage, maintenance history, and real-time operational status to centralize all critical data.
Can Fleet Efficiency integrate with other systems?
Yes, the Fleet Efficiency module synchronizes dynamically with external systems, ensuring seamless data integration for wagon inventory, availability, and operational details.
How does Fleet Efficiency handle wagon-related alerts?
It allows you to configure event-based alerts for critical scenarios such as exceeding inventory thresholds, wagon overloading, or key maintenance events, ensuring timely action to avoid disruptions.
Can I manage wagon availability with the Fleet Efficiency module?
Absolutely, the module provides tools to forecast and monitor wagon availability, set inventory thresholds by type or location, and dynamically update availability status to support better resource allocation.
Does Fleet Efficiency support monitoring wagon mileage and transport history?
Yes, shippers can compute wagon mileage through GPS or infrastructure data and track transport history to analyze patterns, optimize fleet usage, and schedule maintenance more accurately.
How does Fleet Efficiency improve maintenance management?
The Fleet Efficiency module allows shippers to schedule, monitor, and track maintenance tasks, link damages to tickets, and follow maintenance progress to minimize downtime and ensure compliance with legal maintenance requirements.
Can I track my wagons’ real-time position with the Fleet Efficiency module?
Yes, the module enables real-time tracking of wagons using GPS and other tracking sources, along with geofencing features to monitor their movements and locations.
What does the Fleet Efficiency module help shippers achieve?
The module helps shippers optimize wagon utilization, schedule maintenance effectively, monitor fleet status in real time, and reduce operational costs by providing comprehensive tools for fleet management.
Get an overview of all your transport costs with Cost Control & Pay
Manage the costs associated with your rail freight operations, track additional costs and their causes, and optimize your contracts.
Manage planned vs actual transport costs
Learn where to reduce extra costs in your transports and make them more cost efficient.
Manage your penalties and discounts
Apply transparent and fair penalties to ensure an improved quality of service in the future.
Validate your costs with your LSPs
Take back control on your transport costs and reduce transport budgets.