Optimize fulfilment rates by automating train composition
Avoid short trains and achieve maximum capacity by automating train compositions and documenting any loading issues.
What is worse? Repetitive manual tasks or errors due to a lack of coordination?
Time management
Repetitive manual tasks eat away 30% of the time of logistics operators.
Desynchronization
Desynchronized supports like Excel, fax, phone and emails cause loss of information and knowledge.
Outdated information
Outdated information causes errors, delays, and leads to increase in costs.
Automated tasks and centralized communication increase efficiency and cut costs.
Automated routine tasks
Automate routine tasks and optimize the use of resources to improve operational efficiency.
Enhanced visibility
Provide enhanced visibility and control over shipments.
Centralized communication
Centralize communication among stakeholders to facilitate coordination.
Eliminate inefficiencies
Identify and eliminate inefficiencies to reduce costs.
Simplified Operations: automate workflows, digitize consignment notes, and enhance operational visibility
Generate pre filled rail freight consignment notes with any transport partner.
What are the main challenges shippers face when the consignment note is not digitized?
Benefits from automatically generated consignment notes:
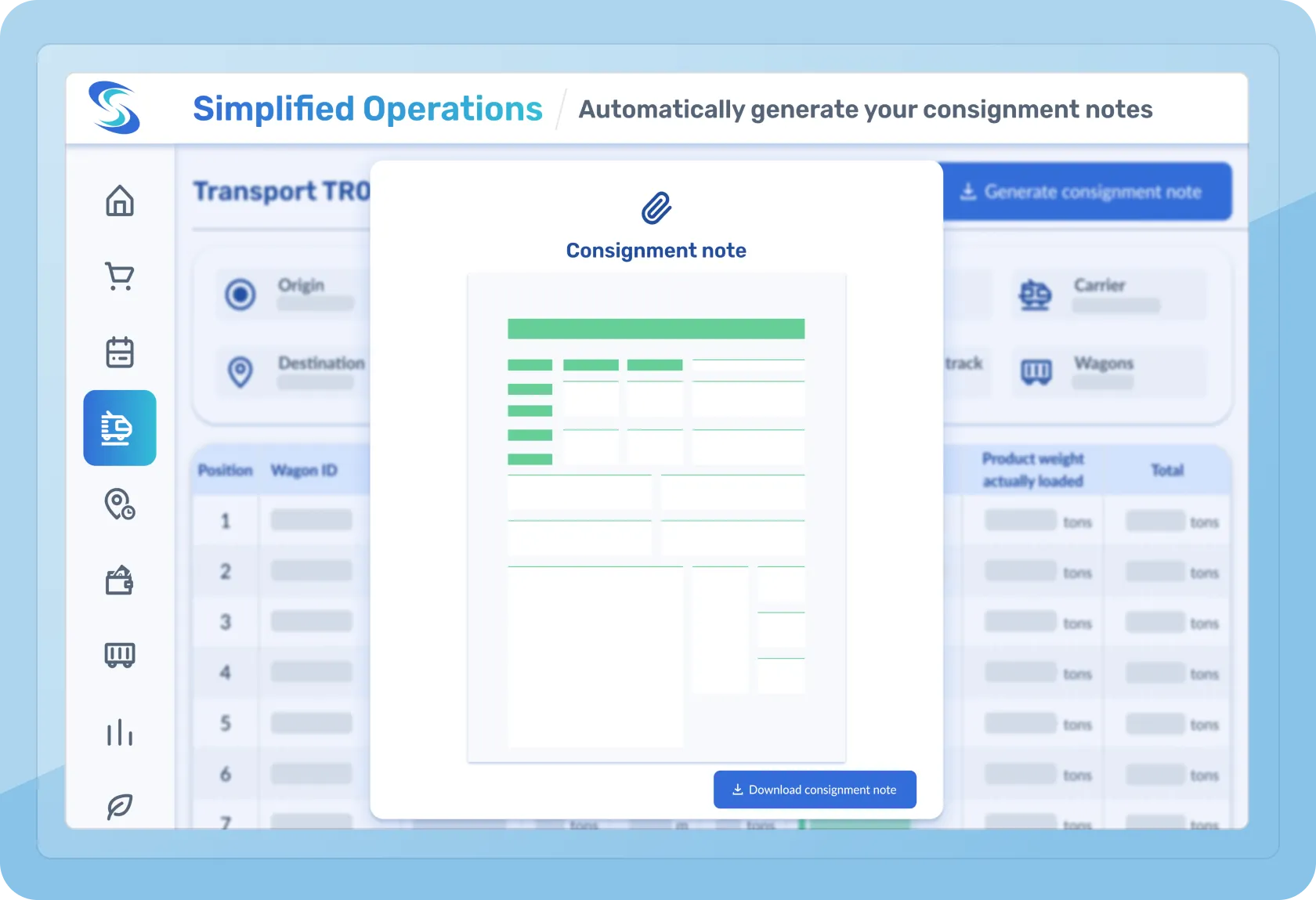
Automate your loading instructions with feasibility checks to anticipate last-minute loading complications.
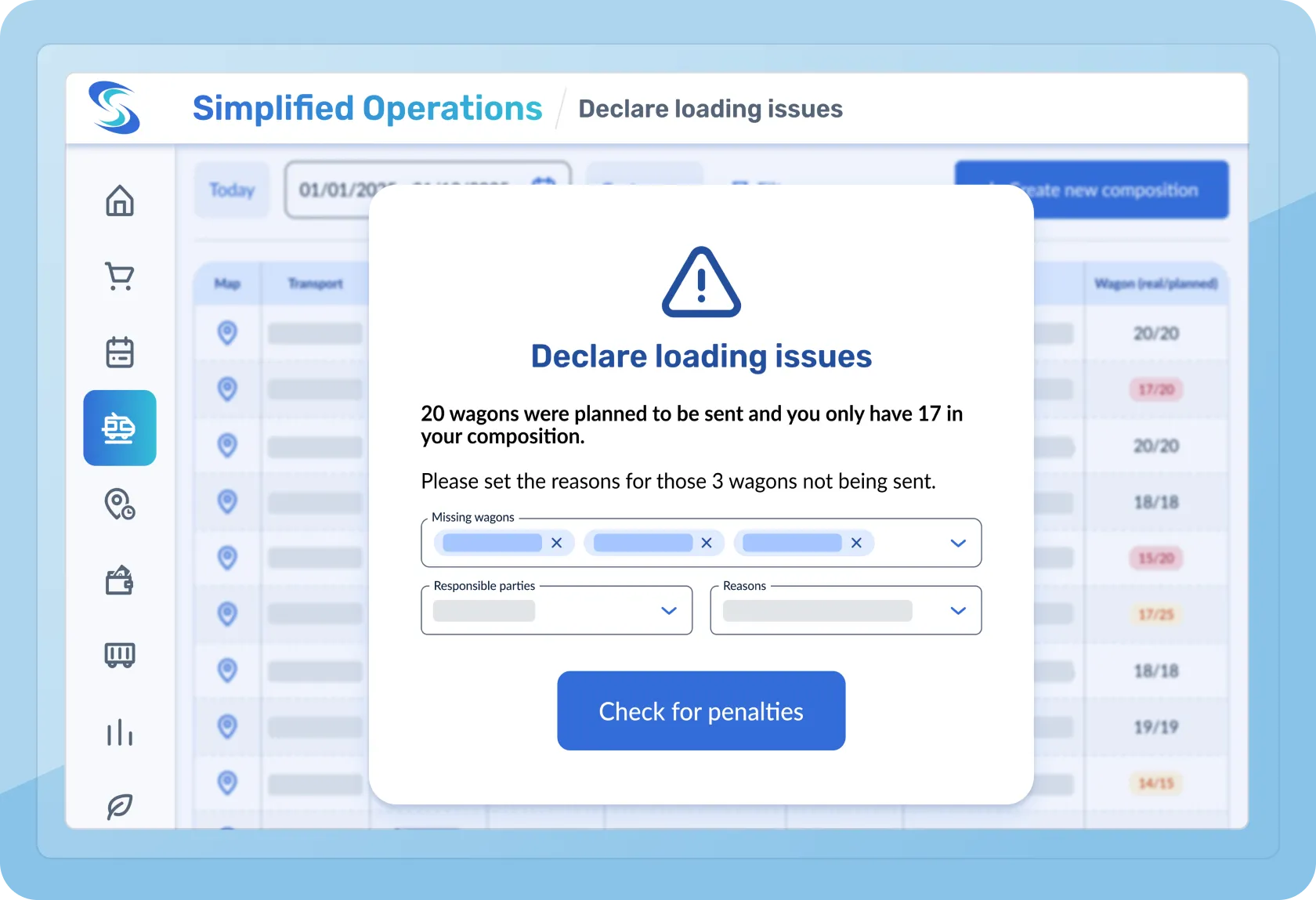
Wagons are ready for loading. What could possibly go wrong?
Avoid wagon loading and unloading issues with a little help from RALF
The more the merrier. But not when it comes to data sources. Unless you integrate composition data directly from your information systems.
Getting different types of data formats under one cover is a tricky challenge
From composition to invoicing with data and systems integration
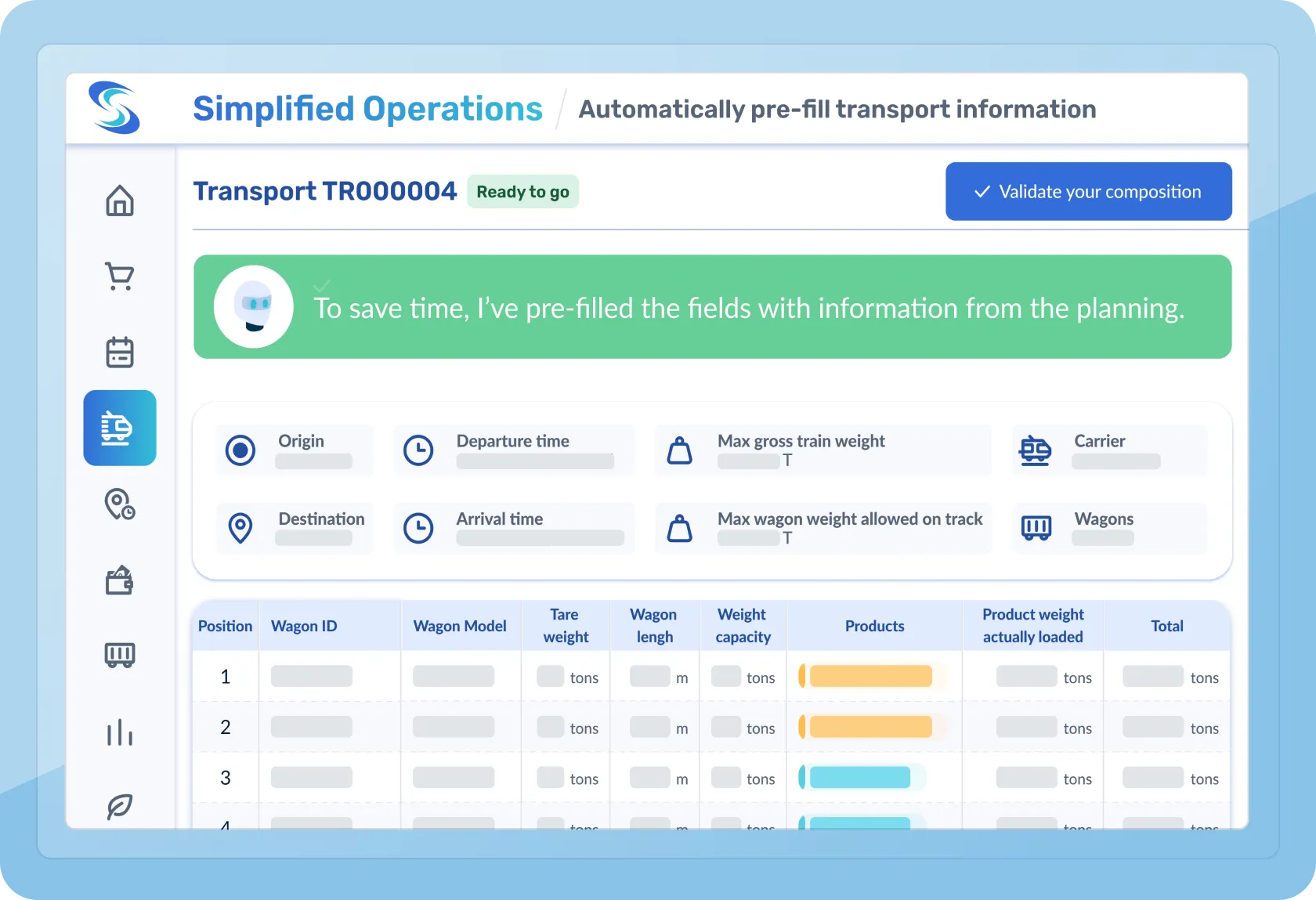
Impacts and ROIs of Simplified Operations on field operations and strategy
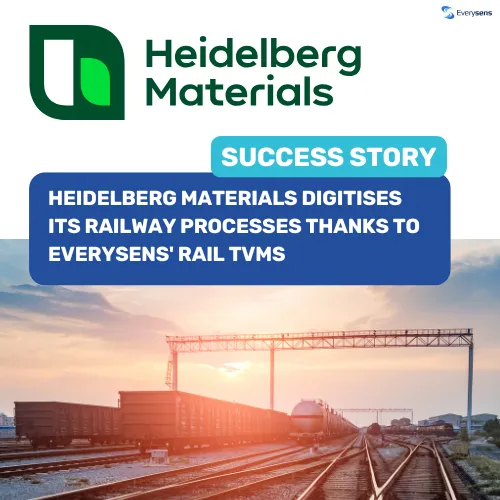
Multiple stakeholders - 1 clean consignment note
Achieve ROI with the following benefits:
Efficiency through automation
Automating the creation and sharing of consignment notes reduces manual tasks, allowing teams to focus on higher-value activities.
Error reduction and data consistency
By eliminating the need for redundant data entry and manual handling, the feature minimizes costly errors and inconsistencies. Fewer mistakes lead to smoother operations and less time spent on corrections or resolving disputes, resulting in cost savings.
Improved collaboration
Reduce delays and miscommunications, leading to more accurate transport planning and resource allocation, optimizing overall logistics performance and cutting transport-related costs.
Take it from our clients
Meet the driving forces that transform the rail freight industry
Hesitations?
Let’s clear them up!
Everything you need to know about Simplified Operations.
How to manage unloading operations in the TVMS?
The TVMS facilitates the coordination and management of unloading activities, as well as declaring any issue during the process. Use it for single and bulk wagons, including tracking unloading progress and ensuring timely completion of operations.
How does the TVMS automate loading instructions?
The TVMS automates the process of providing loading instructions for trains based on consignment details and available resources, optimizing loading efficiency and minimizing errors.
Is there an overview of train compositions?
The TVMS provides a comprehensive view of the entire train composition, including details of each wagon, cargo types, and placement, facilitating better management and operational planning.
Why should loading issues be declared and shared with all stakeholders?
This feature enables users to report and document any loading-related problems or discrepancies encountered during the loading process, ensuring transparency, accountability and timely resolution of issues.
Is it even possible to fully automate the creation and edition of train compositions?
Users can modify or create train compositions manually, while still leveraging automated assistance for optimal configuration. This allows for flexibility in train setup tailored to specific needs or constraints.
What is the use of digitizing contractual specifications for consignment notes?
Allows users to input and manage all contractual details related to consignment notes electronically. It streamlines the process of documenting and adhering to contractual obligations associated with consignments.
Go further with Real-Time Visibility
With Simplified Operations established, the next step is to make your operations more transparent with real-time visibility and improved incident management.
Monitor real-time ETA on a map
Predict ETA for each transport, block train and single wagons, automatically updated at each tracking event.
Follow your transports and their incidents on a map in real time
Know the position and status of each train, wagon and associated products.
Automatically detect tracking events from multiple sources
Get reliable information on your transports from your railway undertaking, GPS and infrastructure.